An Interview with Samantha Melnyk
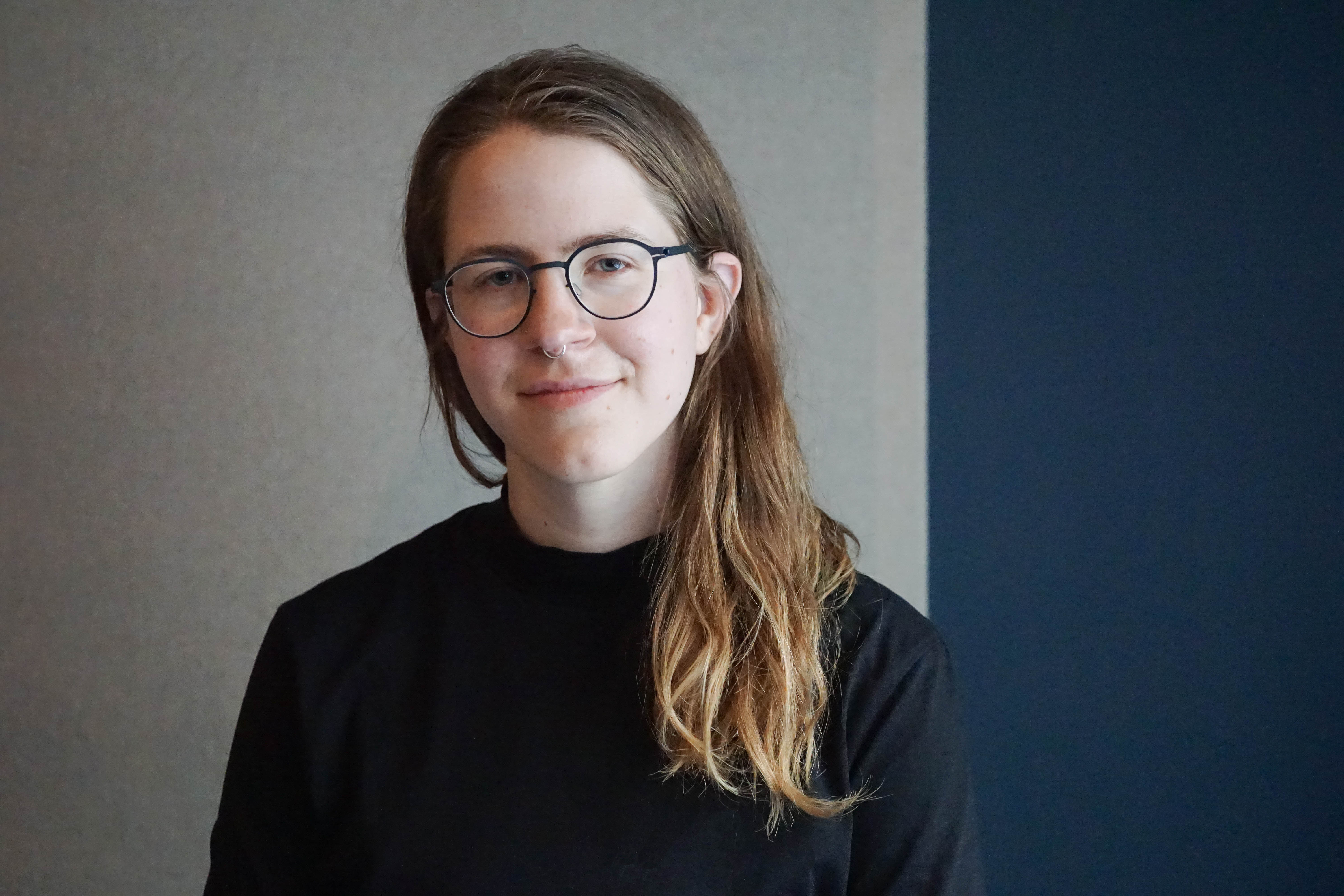
What is your background?
I actually have a background in architectural research, but I have branched into different things such as industrial design, circular design, haptics and digital fabrication. I’ve always had a curiosity about how all sorts of things are made and through living in a few different places in Canada, Germany, and France - I have seen so many fabrication practices and types of values placed into making.
What are your experiences so far being a woman in the music technology field?
While I haven’t been working in music technology for that long, say about two years, I can certainly feel an absence of diversity. I recognized this early on by attending online music tech meetups, going to showcases like Superbooth, and in my own immediate work environment. I am the only person who identifies as a woman on the engineering team at the moment. It is not for a lack of trying to get more diversity hired on the team, but from first-hand experience, it has been difficult to get applications from people with different backgrounds in this industry. We all know there are many factors that actively contribute to this. In the past, I have been lucky enough to be a part of teams that were very diverse. It was such a great and open space to operate in. I have also had the opposite experience of this and it certainly wasn’t something sustainable for me to remain in.
Did you have a role model or mentor?
I worked with a lot of amazing people in my studies, a lot of women in the STEM sector and in architecture. It would be tricky to name them all here. However, I will mention that my partner is a big role model for me. She is an architect, who has been really pushing for environmental progress in the building sector. Through her, I developed a different type of relationship with design and the materials we use. It opened the door to this very complex but important world to navigate to put out more sustainable products. I am bringing these values and this passion for a move to a healthier building practice, the circular economy, into my work at KORG Berlin.
Can you give an example?
Such an example was a project where I was researching and testing sustainable packaging, in particular mycelium packaging. It seemed a good place to start to stop using things like styrofoam (EPS packaging), which has now become synonymous with marine litter. While this highly depends on the location, EPS is rarely recycled for many reasons. Current technology downcycles this material, not keeping it in any circular loop for long, so ultimately it normally just ends up in landfills because it is not attractive economically to do anything else with it. Mycelium packaging is a composite of a cellulose-based material (say hemp offcuts) and mycelium spores. These spores will grow amongst the hemp and fuse this aggregate together. It is a fascinating process with a few more details than this, but in the end, you have completely compostable low-impact packaging. This type of packaging can be very useful for larger keyboard instruments that need extra cushioning when being transported.
How does your day to day look like?
When I initially started at KORG, I was living in Berlin and was onsite in the workshop - I was doing different fabrication tasks like machining with the in-house CNC, 3D printing, etc. I work with a motivated team keen to take on the challenges of the circular economy, so we often have a lot of conversations around this on the industrial and mechanical engineering side of things. At the start of designing the product KORG Berlin is currently developing, material research was a large part of my day-to-day. I got my hands on materials that were of interest to us to work with them first hand, to really see what could fit the product visually, haptically, and conduct early viability studies if the material could work mechanically.
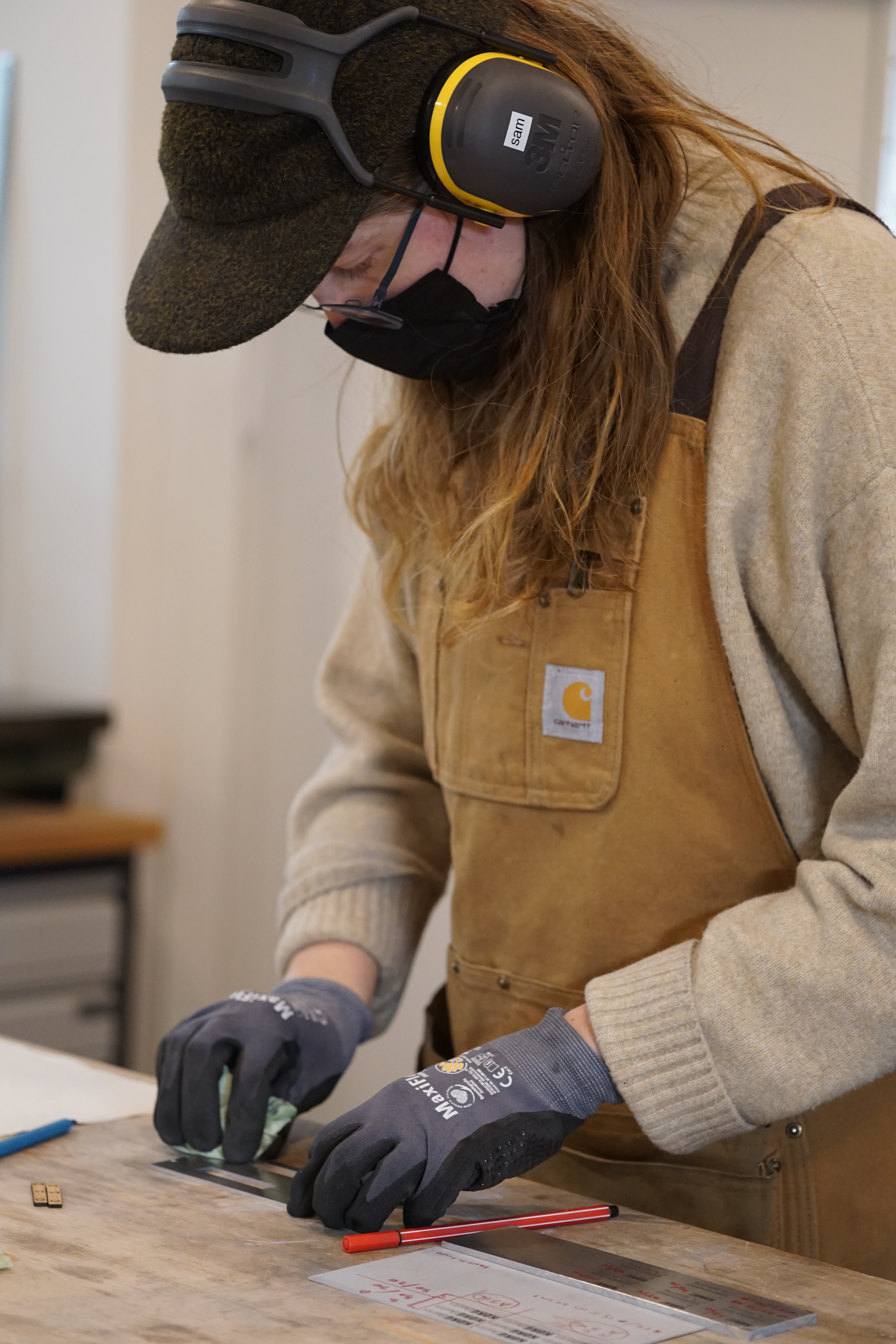
In the last months, I have actually relocated to Montreal, so my role involves no physical fabrication now. I am doing a lot of design and planning work to figure out how the current product in development can remain circular in the manufacturing stage. This involves looking at a giant network of entwined relationships like where materials are sourced, where they have to travel to, the carbon costs of processing this material, the type of energy that is being used in production - I could go on. Another big point of development is to create strategies for people to be able to care for our products and to set up an infrastructure of care that has to run parallel with the product development.
Which materials did you end up using? In terms of shape and color, do you have to stick to certain conventions or are you free to design the items as you wish?
Right now material choice is being driven by what makes sense for endurance and the environment, the two have equal footing in our selection as well as understanding what recycled or recyclable materials are available. In terms of colour, we often say we are trying to work with honest materials, so minimizing any aesthetic treatment while we focus only on treatments that improve the lifespan without jeopardizing recyclability. Things like this are guiding the decisions we are making on the different components of the product.
The idea of care seems quite present in your approach.
I am inspired by the right to repair movement, and like many, I feel it is extremely important that we adopt this into electronic products so we can care for them. These products need to be designed in a way people can maintain them, disassemble them, replace parts and feel comfortable and confident doing this. I think people clearly want to value repair again and we should be able to keep our beloved electronic instruments working and not ending up in a junkyard. Sometimes these repairs are so minor, it could be just a loose connection somewhere, and you should be provided with the resources to be able to troubleshoot this at home. Sometimes they are a bit more involved, like replacing a broken key, and you should be able to have access to a replacement. It is the story same for replacing batteries, screens, or any specialized items for the product.
It has been important for us to also think about the end-of-life strategy for our products. While we hope it takes a long while to come to that, information needs to be accessible in different forms so that wherever this ends up, someone can take it apart and recycle or repurpose it properly.
Will you travel to Europe regularly? How do you collaborate with others in the design process?
For the moment no, and I don’t think we are entertaining this. The way the world is now, I think I will only return to Berlin (or wherever it is necessary to go) for something that really requires a physical presence. I am also not the only remote person on the team, we have set up a system for online people to collaborate with people who are in the office. It involves a good deal of online meetings with debates, discussions, and a lot of sketching digitally or physically with paper being held up to the camera. Everyone puts attention into regular updates and communicating their ideas by posting them on a workplace messenger. I think sometimes having to write your intentions down and be very clear about them has been rather beneficial to make sure we are all on the same page - especially because you can’t always explain it live. I have also been collaborating with researchers and different people outside of KORG Berlin on circularity for the product, the same workflow rings true for them as well. The transition to working entirely remote has been relatively painless since many of us have had good practice with seeing our coworkers solely online over these past few years.
What advice would you give to women who are pursuing a career in music technology?
I think we all need to be vocal about wanting more diversity in the fields that clearly lack it. I would love to see more and more of this in music tech, it will only enrich the community. I hope people can feel confident enough to jump into these spaces, despite any conflict they might feel with their suitability or background. Ignore that voice. Sometimes we haven’t been built up or encouraged in the same way as those who are more visible in the scene, but our voices need to get out there.
Thank you!
This interview was conducted live in Berlin in August 2021 and online in 2022.